This section will cover achieving consistency in electrical supply, metal melting, sampling and sampling supplies, electrical and chemical calibration, and instrumentation so as to achieve the most accurate and repeatable thermal analysis measurements.
Thermal analysis (TA) is a method of determining chemistry and microstructure in complex metals by measuring thermal arrests, and energy production during solidification, and sometimes energy production during solid state transformations. The temperatures of multiple arrests and the rate of change in temperature at various points are measured by means of an embedded thermal couple. The thermal couple produces a temperature dependent voltage which is converted to digital format and processed by a Microprocessor or by a personal computer to produce the results.
In the production of irons, TA is commonly used to measure Carbon Equivalent, Carbon and silicon. Less common uses include graphite morphology for gray, compacted and ductile irons, the degree of inoculation, the degree of chill, and the degree of pearlite/ferrite in final irons, and the effective magnesium in ductile and compacted graphitic irons. In white irons, where graphite production must be very tightly controlled, TA provides a comparison with production iron vs. 100% chilled iron.
In the production of aluminum alloys, TA is commonly used to measure the degree of inoculation and modification of hypoeutectic-silicon alloys (A319, A320, A355, A356 etc), and the degree of nucleation of A200 series and hypereutectic silicon alloys.
In the production of Copper alloys, TA is commonly used to measure the phosphorus levels for brazing alloys, and for high phosphorus copper alloys up to about 15%.
In steel production, TA is used to measure low carbon levels in low alloy steels, and to measure correct carbide levels in wear resistant alloys.
Applications
Thermocouples are most suitable for measuring over a large temperature range, up to 1800 °C. They are less suitable for applications where smaller temperature differences need to be measured with high accuracy, for example the range 0--100 °C with 0.1 °C accuracy. For such applications, thermostats and RTDs are more suitable.
Temperature measurement techniques
In the ferrous foundries ladle temperature varies above 1700 C.
At this temperature continuous measurement is difficult. Therefore dip type immersion pyrometer technique is widely used.
Immersion pyrometer consist of metal housing, Electronic Measurement Circuitry (EMC), metal lance, Thermocouple connected to the circuitry by means of compensating cables which passes through the lance.
When thermocouple dip into the molten metal, it gives milli-volts output. These milli volts are carried to the EMC, where the signal (mv) is amplified and processed to give direct digital output. The processing of the signal is done by various techniques. Peak latching, Plateau Detection, Continuous tracking are some of these techniques.
Peak Latching:
As the name indicates the technique involves latching of the peak temperature and displaying it. In an induction furnace due to its nature hot spots are generated that moves randomly across the molten metal. Generally the temperature at the hot spot is always higher than the molten metal temperature. If the Thermocouple comes into contact with the hot spot then this reading is latched by the EMC and displayed. Thus temperature at the hot spot is not correct representation of the entire bath temperature. Therefore peak latching is not world wide accepted for use in measuring molten metal temperature in induction furnaces.
Continuous tracking:
In this technique temperature is displayed continuously as it senses. So you do not get stable display of temperature. So it is difficult to know, when to remove lance. Temperature recording is fully dependent on operator skill and it can not separate out hot spot temperature and true temperature. So it is not suitable for ferrous foundries.
Plateau detection technique:
In this technique transient response of sensor and system is ignored. Steady state response is monitored and confirmed by taking several samples. Once it fits in its detection criteria the temperature is displayed. The operator can remove the lance to prevent it from melting in the molten metal bath. This technique displays correct temperature and ignores incorrect readings by giving error messages. Thus there is no possibility of hot spot measurement in this technique. This operation is completed in 1-3 sec in case of single dip paper tube thermocouple tips and 3-8 sec in case of Multi dip thermocouple tips. It ensures life of receptacle (connector for tip and lance).
Transient response phenomenon is very common term in the field of process instrumentation i.e. how system (including sensor) responds for any sudden change is characterized by this terminology.
In case of Immersion Pyrometer, as we are suddenly inserting thermocouple inside the molten metal bath; its response could be like shown in Fig 1 or Fig 2 as it depends on various factors.
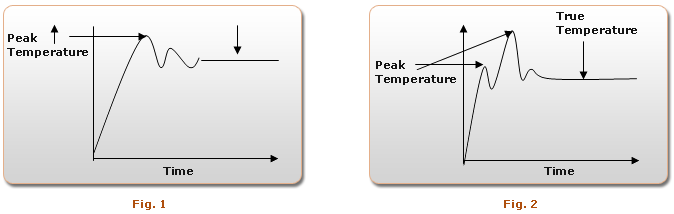
Normal track mode, time based & peak latch temperature indicator fails to identify & measure the true temperature.
For molten metal temperature measurement only, Plateau detection technique is recommended & accepted worldwide, In case, if there is a HOT SPOT with molten metal in the furnace, the temperature at HOT SPOT is more than the rest of the molten metal.
If you are using ordinary PEAK LATCH INDICATOR type pyrometer, it displays this HOT SPOT temperature, which may be more by 20-25 degree centigrade. In such condition you may face the problem of COLD POURING, as the actual temperature is less by 20-25 deg.
But in case of PLATEAU DETECTION TECHNIQUE, as soon as thermocouple is dipped into molten metal, first peak temperature is ignored and it ensures 7 constant readings for a period of one second & declares true temperature readings. It ignores false readings due to furnace hot spot, noise, and transient response & once it detects steady state temperature i.e. flat temperature it will be displayed.
How Does a Thermocouple Tip Works
It is important to note that thermocouples measure the temperature difference between two points, not absolute temperature.
In most applications, one of the junctions — the cold junction— is maintained at a known (reference) temperature, while the other end is attached to a probe. For example, in the image below, the cold junction will be at copper tracks on the circuit board.
Another temperature sensor will measure the temperature at this point, so that the temperature at the probe tip can be calculated.
Thermocouples can be connected in series with each other to form a thermopile, where all the hot junctions are exposed to the higher temperature and all the cold junctions to a lower temperature. Thus, the voltages of the individual thermocouple add up, which allows for a larger voltage.
Having available a known temperature cold junction, while useful for laboratory calibrations, is simply not convenient for most directly connected indicating and control instruments. They incorporate into their circuits an artificial cold junction using some other thermally sensitive device (such as a thermister or diode) to measure the temperature of the input connections at the instrument, with special care being taken to minimize any temperature gradient between terminals. Hence, the voltage from a known cold junction can be simulated, and the appropriate correction applied. This is known as cold junction compensation.
Usually the thermocouple is attached to the indicating device by a special wire known as the compensating or extension cable. The terms are specific. Extension cable uses wires of nominally the same conductors as used at the thermocouple itself. These cables are less costly than thermocouple wire, although not cheap, and are usually produced in a convenient form for carrying over long distances - typically as flexible insulated wiring or multi core cables. They are usually specified for accuracy over a more restricted temperature range than the thermocouple wires. They are recommended for best accuracy.
Compensating cables on the other hand, are less precise, but cheaper. They use quite different, relatively low cost alloy conductor materials whose net thermoelectric coefficients are similar to those of the thermocouple in question (over a limited range of temperatures), but which do not match them quite as faithfully as extension cables. The combination develops similar outputs to those of the thermocouple, but the operating temperature range of the compensating cable is restricted to keep the mismatch errors acceptably small.
The extension cable or compensating cable must be selected to match the thermocouple. It generates a voltage proportional to the difference between the hot junction and cold junction, and is connected in the correct polarity so that the additional voltage is added to the thermocouple voltage, compensating for the temperature difference between the hot and cold junctions.
Different types of Thermocouple
A variety of thermocouples are available, suitable for different measuring applications (industrial, scientific, food temperature, medical research, etc.).
Type K (Chromel (Ni-Cr alloy) / Alumel (Ni-Al alloy)): The "general purpose" thermocouple. It is low cost and, owing to its popularity, it is available in a wide variety of probes. They are available in the −200 °C to +1200 °C range. The type K was specified at a time when metallurgy was nowhere near as advanced as today and consequently characteristics vary considerably between examples. There is another problem in that one of the constituent metals is magnetic (Nickel). The characteristic of the thermocouple undergoes a step change when a magnetic material reaches its Curie point. This occurs for this thermocouple at 354°C. Sensitivity is approximately 41 µV/°C.
Type E (Chromel / Constantan (Cu-Ni alloy)): Type E has a high output (68 µV/°C) which makes it well suited to low temperature (cryogenic) use. Another property is that it is non-magnetic. Type J (Iron / Constantan): Limited range (−40 to +750 °C) makes type J less popular than type K. The main application is with old equipment that cannot accept modern thermocouples. J types cannot be used above 760 °C as an abrupt magnetic transformation causes permanent de-calibration. Type J's have a sensitivity of ~52 µV/°C .
Type N (Nicrosil (Ni-Cr-Si alloy) / Nisil (Ni-Si alloy)): High stability and resistance to high temperature oxidation makes type N suitable for high temperature measurements without the cost of platinum (B, R, S) types. They can withstand temperatures above 1200 °C.
Sensitivity is about 39 µV/°C at 900°C, slightly lower than a Type K. Designed to be an improved type K, it is becoming more popular.
Thermocouple types B, R, and S are all noble metal thermocouples and exhibit similar characteristics. They are the most stable of all thermocouples, but due to their low sensitivity (approximately 10 µV/°C) they are usually only used for high temperature measurement (>300 °C).
Type B (Platinum-Rhodium/Pt-Rh): Suited for high temperature measurements up to 1800 °C. Unusually type B thermocouples (due to the shape of their temperature-voltage curve) give the same output at 0 °C and 42 °C. This makes them useless below 50 °C.
Type R (Platinum /Platinum with 13% Rhodium): Suited for high temperature measurements up to 1600 °C. Low sensitivity (10 µV/°C) and high cost makes them unsuitable for general purpose use.
Type S (Platinum /Platinum with 10% Rhodium): Suited for high temperature measurements up to 1600 °C. Low sensitivity (10 µV/°C) and high cost makes them unsuitable for general purpose use. Due to its high stability type S is used as the standard of calibration for the melting point of gold (1064.43 °C).
Type T (Copper / Constantan): Suited for measurements in the −200 to 350 °C range. The positive conductor is made of copper, and the negative conductor is made of constantan. Often used as a differential measurement since only copper wire touches the probes. Type T thermocouples have a sensitivity of ~ 43 µV/°C.
Thermocouples are usually selected to ensure that the measuring equipment does not limit the range of temperatures that can be measured. Note that thermocouples with low sensitivity (B, R, and S) have a correspondingly lower resolution.
Type B, S, R and K thermocouples are used extensively in the steel and iron industry to monitor temperatures and chemistry throughout the steel making process. Disposable, immersible, Type S thermocouples are regularly used in the electric arc furnace process to accurately measure the steel temperature before tapping. The cooling curve of a small steel sample can be analyzed and used to estimate the carbon content of molten steel.
Electrical Grounding
The TA instrument is measuring 0.0 to 0.018 volts when using S or R type thermocouple and 0.0 to 0.055 volts when using K type thermocouple. The raw precision is generally listed at 0.1 degree C which can be improved through software filtering to about 0.05 degrees C. To achieve this degree, it is important to have a good ground for reference. Neutral lines typically have as much as ½ volt of induced energy in them. That is, the electrical noise in the lines can be equal to or greater than the signal we are trying to measure.
Long runs of thermocouple wire mean more susceptibility to picking up electromagnetic energy. The power pickup shoes of an overhead crane were arcing between rail segments in one foundry causing a pickup of energy equivalent to 10 degrees C of temperature. Running a shielded thermocouple wire solved the problem.
Metal Consistency
Thermal Analysis looks at the transitions between liquid and solid metal. To measure the effect of any element in the metal, that element must be dissolved in the liquid.
Undissolved crystals, while they may promote nucleation, can throw off the Chemistry Analysis. As a general rule, iron should be heated above 2550 F or 1400 C before it is sampled. This allows the silicon to go into solution. Once the iron has been heated above this temperature, it can be cooled down to lower temperatures and still successfully measured as all the silicon is now in solution.
Similar problems exist with Carbon and Silicon Carbide additions. Silicon Carbide dissolves over time and cannot be measured by TA until it is dissolved. One foundry was adding 4% silicon carbide to a cupola that was feeding into a 10 ton holding furnace. The cupola bed was low, and the holding furnace was almost empty when the TA and the chill wedges showed low silicon. The spectrometer reported the silicon as being within range. It was suspected that the silicon carbide had not finished dissolving, and when the castings turned out hard at shakeout, they were sent back to the cupola for re-melting rather than try to machine them with undissolved silicon carbide in the iron. Likewise Carbon floating on the surface of the furnace can create a
Carbon rich layer if the furnace is not powered on. Generally try to not sample through a carbon or slag layer. Clear a clean spot on the surface, and wash the sample spoon clean of any remains left geometric center of cup due to rapid cooling in the base of the cup.
Sampler consistency
Some types of analysis depend on measuring the cooling rates of the sample. These rates and even the arrest points can be influenced by how full the sample cup is. Sample cups that are filled to less than 1 cm or 1/3 inch below the top are suspect. The thermocouple needs to be in the center of heat of the metal mass. This point is slightly above the geometric center of cup due to rapid cooling in the base of the cup.
Samplers can also fail. This usually means that the thermal couple can melt, or come in contact with the metal. The K type of thermal couple is subject to melting when
Sampling molten iron. The TC melts at 2540 F or 1390 C. Since Iron is generally much hotter than that, we depend on a certain amount of temperature loss in transferring the
sample , and in temperature loss to the cup before the thermocouple reaches its max. The twisted thermal couple has good mechanical bonding and will only fail if the ceramic tube cracks or the core wash over the TC is thin or missing, or the melting point is reached. The quartz tube style cup can fail if the quartz breaks, or if the wire softens enough. Due to the connection with the cup stand, the wire is in tension, and can pull apart if the joint softens enough. The wire will pull away from one side of the cup about ½ centimeters. This will typically terminate the analysis.
Calibration consistency
Many foundries make life hard for themselves by over calibration. Deming pointed out that this can be a major source of error, and TA proves the point. First the calibrator has an internal temperature sensor that corrects for differences between room temperature and the melting point of ice. This sensor is embedded inside of the instrument and can be fooled. If the calibrator was stored in an air conditioned (summer) or heated (winter) office, the cold junction sensor can be off by 10 to 15 degrees C.
Both the calibrator and the metal pins/rails of the cup stand need to be at room temperature to avoid errors. People who calibrate too often end up taking shortcuts and introduce errors into the calibration by not letting the calibrator and or stand heads come to room temperature: an operation that can take up to 30 minutes depending on the instrument. It is best if proper care is taken in the calibration, and then no further calibration is done until there is an assignable cause (damage or replacement of components) or the time period is expired for the calibration (usually 6 months).
Instrument calculation consistency
Thermal analysis is limited by some mathematical constraints called the degrees of freedom. Typically for example, in iron, we calculate chemistry from two data points and try to solve for Carbon and Silicon. Actually Carbon, Silicon, Phosphorus, Manganese and Chromium all affect the arrest points. To calculate silicon, it has to be assumed that phosphorus, manganese and chromium remain relatively consistent or that the change in those elements is insignificant. Manganese is the usual culprit when
the silicon analysis varies. The handbook equation is C.E. = Carbon + Silicon/3 + Phosphorus/2 + Manganese/5 - Chromium/ 9. In actuality we generally find the silicon
factor to vary between 2.5 and 3.3 depending on iron type. General practice is to determine the best silicon equation for each major metal type. A major metal type would be those that had significantly different levels of manganese, phosphorus, or
chromium. Carbon analysis agrees with combustion analysis to within the typical error of combustion analysis, so it is hard to tell which one is more correct.
Carbon Equivalent analysis is defined by the TA measurement. That is C.E. is determined by the Liquidus temperature. Some people confuse the issue by thinking that by using the spectrometer chemistry in a formula that they can calculate the C.E. and therefore what the Liquidus temperature should be. That is not so. The calculations using chemistry are approximant.
The actual measurement of the Liquidus is exact. In the old days the Liquidus temperature was used to measure the fluidity of the metal (lower temperature implied more fluidity). This was an improvement on the fluidity spiral which could be affected by temperature or wetness of the mold.
Conclusion
Mathematically the standard error of a system is the square root of the sum of the squares of all the errors. It might be daunting to some to see all the sources of error possible. But with good engineering, a good instrument, and a good lab, it is possible for most foundries to benefit from the use of TA. In practice the amount of error varies from foundry to foundry. But generally a standard error of 0.03% carbon and 0.03% silicon can be obtained if these guidelines are followed. This compares with lab results of 0.035% for combustion carbon and 0.02% for spectrometer silicon.
|